Guissona Food Corporation automates its animal feed plant in Bujaraloz
ISA S88 standard implemented by incorporating the PlantPAx™ process control solution; enhancing flexibility, standardising industrial processes and improving performance.
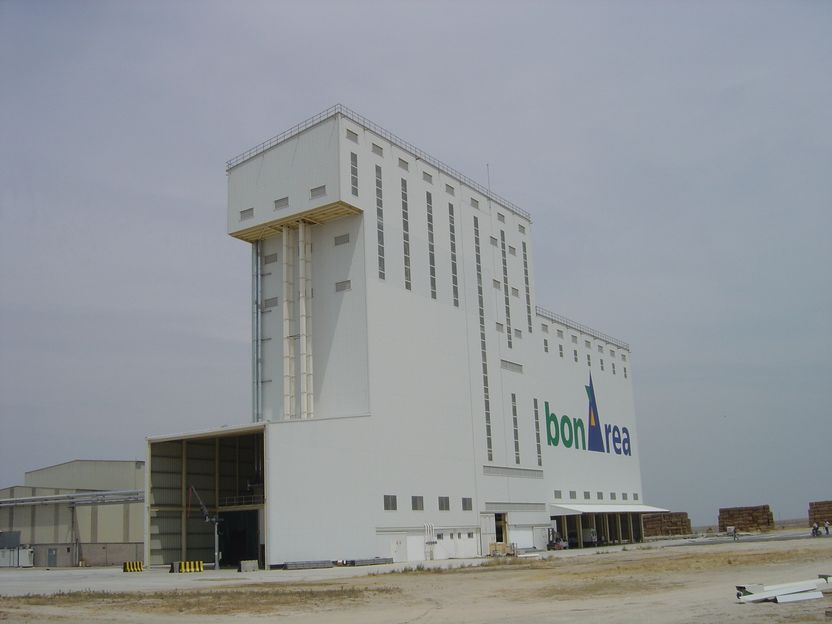
Rockwell Automation GmbH
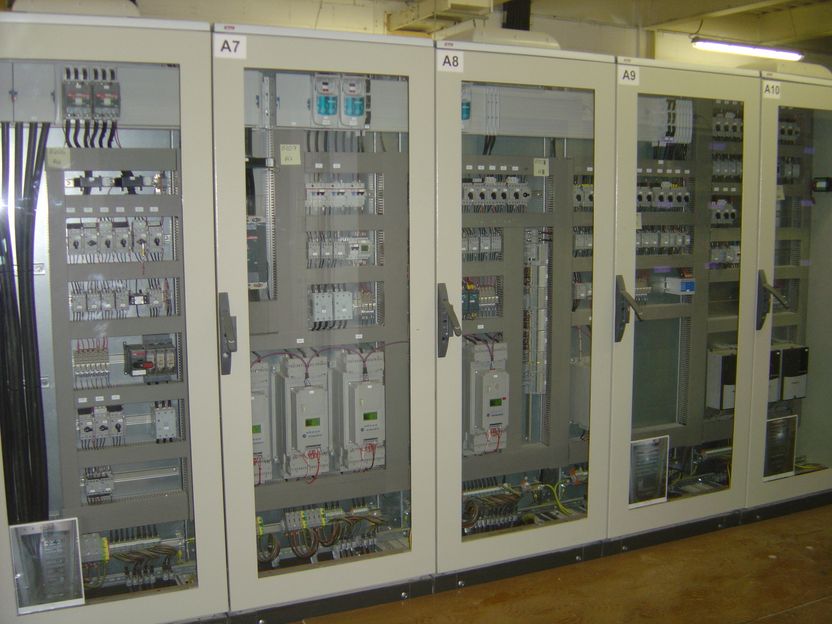
Rockwell Automation GmbH
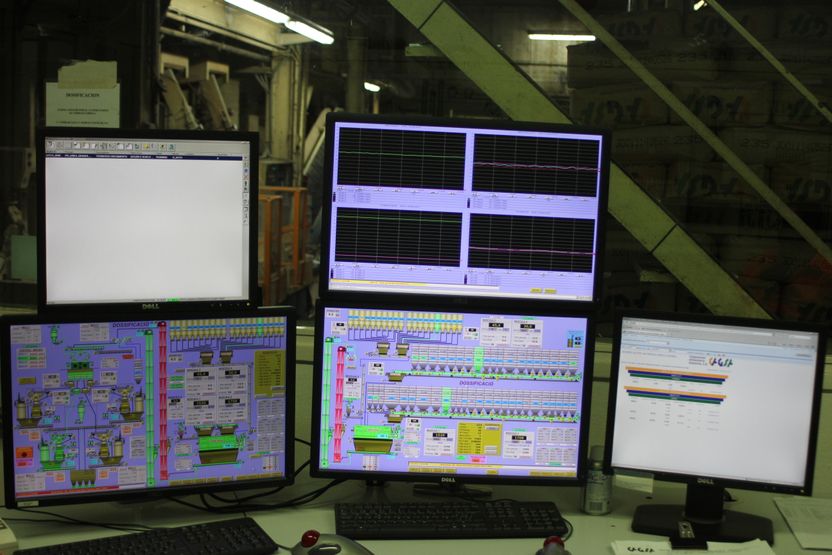
Rockwell Automation GmbH
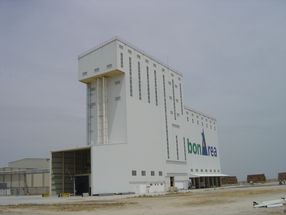
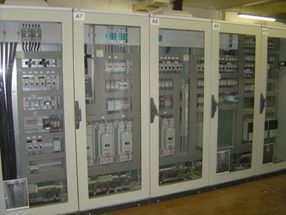
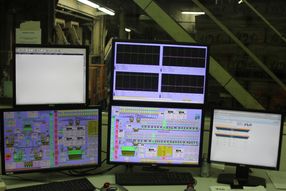
Background
Guissona is one of Catalonia’s leading food companies and has been in business for over fifty years. The company raises livestock and performs its industrial and commercial processes with such thoroughness that the product is able to reach consumers directly, without the need for middlemen.
Guissona is involved in a wide range of activities including: the breeding of poultry and livestock; manufacturing of animal feed; breeding, fattening and slaughtering of animals; processing and preparation of different food products; and the distribution and direct selling of its products in over 400+ BonÀrea stores.
The goal of Guissona is to improve the productivity of its livestock farms and also cater to the needs of its customers, who have embraced their efficacy and savoir faire. The Company enjoys a strong reputation for producing a variety of safe, high-quality and reasonably priced products for its customers. To strengthen this brand reputation, the corporation boasts cutting-edge facilities and a team of dedicated professionals. As a testament to this recognition, Guissona has been awarded the ISO 9002 certification for its high standards of production, installation and servicing; the ISO 22000 certification for the highest levels of safety of their meat-based products; and the ISO 14001 certification for its environmental management.
For about fifteen years, Guissona has teamed with Rockwell Automation to incorporate its solutions in various animal feed manufacturing and processing plants. More significantly, in 2009, the organisation opened a facility in Bujaraloz (Zaragoza), which integrates the latest industrial automation technology.
Challenge
Since its adoption in 1995, the ISA S88 standard has served to guide the implementation of batch-based process control systems in production centres, allowing high levels of flexibility and reusability. When Guissona established its new Bujaraloz factory, it decided to implement the ISA S88 standards across the entire facility—to help reduce the costs, engineering efforts and time-to-market; while improving flexibility and enhancing process quality.
“The Automation Manager of the Animal Foods department explains: “This move was a great challenge for us as it was the first time that we had implemented a batch system in our facilities. For that reason, we decided on the Rockwell Automation PlantPAx™ process automation system. This allowed us to fully utilise our installed capacity and increased the flexibility in the way that we could edit recipes, either by the team in charge of formulation or by the software designed for that purpose.
“Another important challenge,” he continues, “was the integration with our ERP system to enable us to correctly send and receive order information—without forgetting “the importance of materials management and traceability.”
Solution
From the beginning, Guissona decided to implement the PlantPAx process control solution from Rockwell Automation, which provides high availability, ease of device integration and asset management, batch and sequencing control and improved design and operations productivity.
Through the use of the PlantPAx™ system, Guissona saw improvements in three areas: production management, materials inventory and historical data. According to the Automation Manager of the Animal Feed Department, “The first area of improvement was in production management. The new MES application was designed to create production batches from order information from the ERP system and automatically send it to the batch manager.” He further stated, “We also decided to improve the performance of our production process to allow us to focus on our materials inventory and provide us with real-time information on stock levels, location and availability. We also generated a batch, consumption and traceability reporting system based on the historical data furnished to us. We accomplished this through the PlantPAx system and its batch software”.
The new process control system, together with the MES application, allow Guissona to monitor the 153 equipment phases established for the plant. In addition, the PlantPAx system was easily integrated to 140 variable-frequency drives, several soft motor starters and 16 weighing systems, each of which includes five scales that assist the variable-frequency drives in controlling the different dosage regimens to be administered to each plant.
Results
According to the Automation Manager: “The batch system has made it easier for us to upgrade all our resources and transform our facility into a phase-based operation. This has enabled stricter operational control, more efficient workload sharing and more effective planning. Now, everything follows the batch standards, helping administration and subsequent maintenance operations.”
Thus, he continues: “We saved time programming ControlLogix® and execution was made using batch, which controls and manages the different tasks.
“In addition, by utilising the ISA S88 standards, we have reduced the time to develop and maintain the system and enhanced its performance. It has also given the company greater flexibility in modifying and creating new products in the plant, providing accurate information about materials in stock and production levels, improving batch follow-up and tracking, and enabling the creation of reports on any of its processes.”