The effective cleaning concept for shell moulding lines
"EasyClean": EASY, QUICK, CLEAN!
Advertisement
In confectionery production, shell moulding lines are used for the manufacturing of filled or solid chocolate products. By nature, during production a number of machine parts come into contact with the production masses and need to be cleaned after some time. Depending on the manufacturer and type of the production line, this can be a time-consuming job, causing down-times and often demanding a great deal from the cleaning staff.
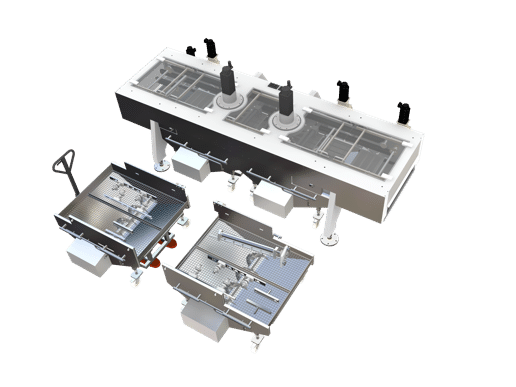
orbital shell former with second set of exchange parts
Winkler und Dünnebier Süßwarenmaschinen GmbH
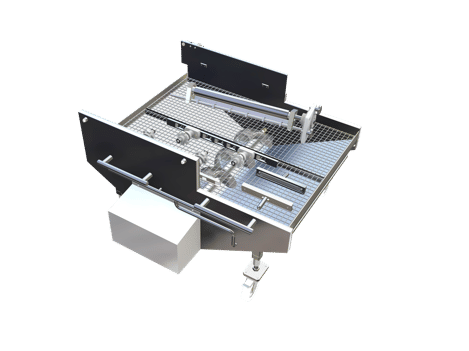
chocolate trough of the orbital shell former with exchange parts placed onto it
Winkler und Dünnebier Süßwarenmaschinen GmbH
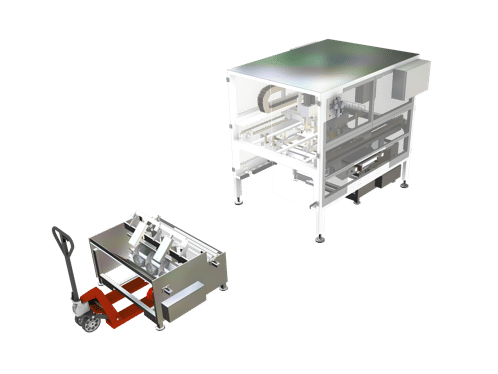
scraper station with extracted chocolate trough
Winkler und Dünnebier Süßwarenmaschinen GmbH
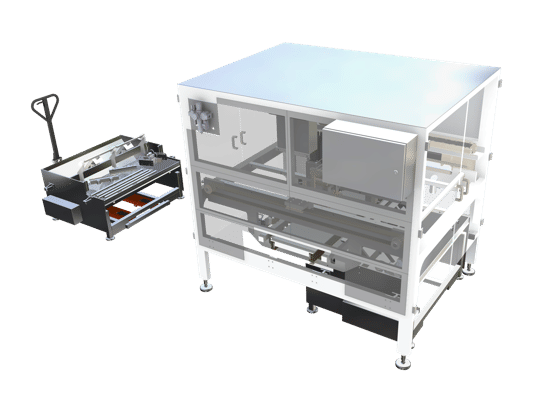
scraper station with extracted chocolate trough
Winkler und Dünnebier Süßwarenmaschinen GmbH
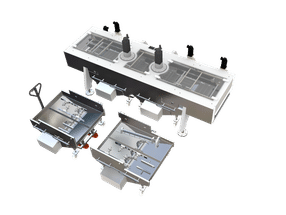
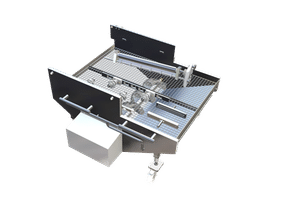
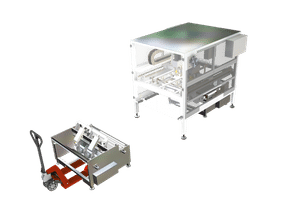
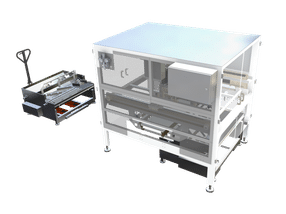
Winkler und Dünnebier Süßwarenmaschinen GmbH shows with its “EasyClean” concept that there is another way: quick cleaning with higher quality and least possible changeover times.
Quick, easy and thorough cleaning – how can this be achieved?
On the basis of a Winkler und Dünnebier shell moulding line type Confec, the “EasyClean” concept can be illustrated as an example. The centrifugal shell-forming station as well as the scraping station of the production line are equipped with chocolate troughs, which can be easily extracted from the respective stations in case of a cleaning cycle or product change.
The procedure is basically always the same at the different stations. In case of the centrifugal shell-forming station for example, at first the chocolate trough is disconnected with quick couplings from its heating and electricity. After the trough has been extracted from the line and a storage grid has been positioned onto it, the dirty parts can be positioned on the grid. The disassembly and re-assembly of all parts in connection with the production masses can be effected without tools in an ergonomic and simple way.
The trough with the parts is now brought on its own wheels or with a lifting cart to the cleaning site for washing there. The cleaning works at the line itself are reduced to the absolutely necessary.
“Clean” in only 15 minutes
It makes sense to have available a second set of exchange parts for an on-the-fly exchange and thereby reduction of the total time required to only 15 minutes – an enormous advantage as the unbeloved machine down-times can thereby be reduced drastically. Besides the time savings “EasyClean” also allows for a considerably improved cleaning result, as the dismantled parts can be cleaned effectively and thoroughly besides the line.
Winkler und Dünnebier provides this concept for all components in direct contact with the production masses. The development which has been started for the depositors has now been consequently continued for other components.
Other news from the department research and development
Most read news
More news from our other portals
See the theme worlds for related content
Topic world Hygiene
Hygiene is the foundation of the food and beverage industry. Hygiene technology ensures that products are not only tasty, but most importantly, safe for consumption. From advanced cleaning processes to sterile filling techniques, the industry is constantly setting new standards to prevent contamination and the growth of microorganisms.
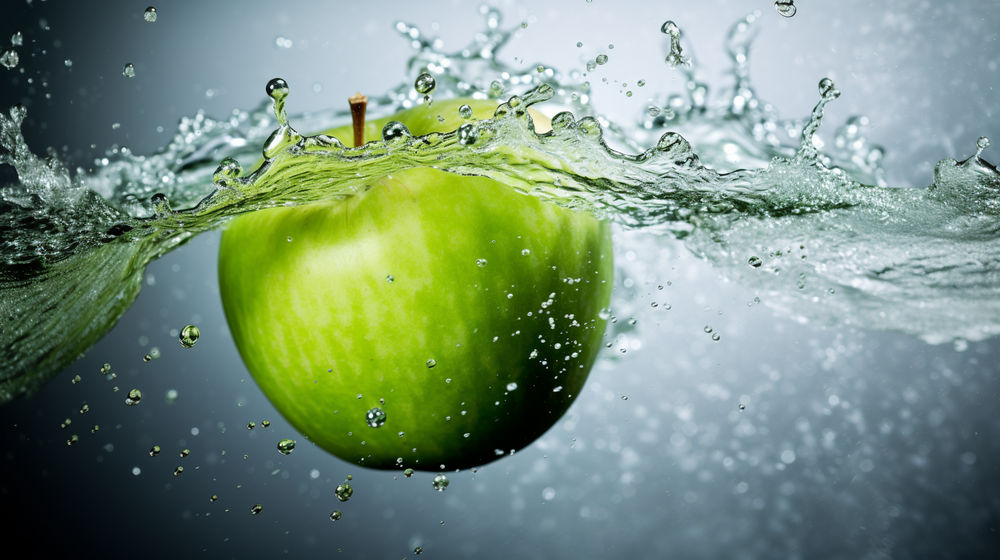
Topic world Hygiene
Hygiene is the foundation of the food and beverage industry. Hygiene technology ensures that products are not only tasty, but most importantly, safe for consumption. From advanced cleaning processes to sterile filling techniques, the industry is constantly setting new standards to prevent contamination and the growth of microorganisms.