Heineken integra la tecnología de impresión 3D en el diseño de componenetes de sus fábricas
Es la primera cervecera española que aplica este innovador modelo de fabricación propia desarrollado junto a Ultimaker, logrando importantes beneficios en la optimización, eficiencia y seguridad de los procesos de envasado de su planta de Sevilla.
-
Ante los excelentes resultados de la primera fase de este proyecto, que desprenden un ahorro en costes del 80% respecto a otros modelos de producción, la compañía valora su escalabilidad a otras fábricas de todo el mundo y a otras modalidades de aplicación.
HEINEKEN España culmina la implantación de un proyecto piloto desarrollado junto a Ultimaker -líder global en el sector de las impresoras 3D- para integrar la tecnología de impresión 3D en el diseño de componentes de sus fábricas. Esta fórmula de fabricación propia supone una importante revolución para la industria de gran consumo por su capacidad para optimizar y mejorar la eficiencia de los procesos productivos, en cualquier sector de actividad. La iniciativa, que demuestra una vez más la capacidad de HEINEKEN para impulsar la transformación del sector cervecero español, sitúa a la compañía a la vanguardia industrial en un ámbito que hasta ahora parecía limitado a campos como el energético, el aeroespacial, el sanitario o la automoción.
El proyecto de HEINEKEN, desarrollado en una primera fase en la fábrica de Sevilla, se ha centrado en varios modelos de piezas para maquinaria de las líneas de envasado. La planta hispalense es la de mayor capacidad de las que tiene HEINEKEN en España con capacidad de producir anualmente 400 millones de litros de cerveza, de marcas tan reconocidas como Heineken®, Cruzcampo, Amstel o Desperados. En tan solo un año, los resultados de esta fabricación “a golpe de clic” con la impresora 3D S5 de Ultimaker desprenden un ahorro en costes del 80% respecto a otros modelos de producción y un impacto positivo en el medioambiente, al reducir los procesos de logística y transporte. Además de las ventajas que supone el poder rediseñar piezas para optimizar la maquinaria a corto plazo, HEINEKEN ha registrado un importante descenso en los tiempos empleados para fabricar cada componente y unos altos estándares en cuanto a funcionalidad y seguridad.
Juan Candau, director de la fábrica de Sevilla, explica: “La impresión 3D ha demostrado ser una tecnología que nos aporta valor y nos permite trabajar más eficientemente, reemplazando componentes bajo demanda, en menos tiempo y a un coste menor que si fueran importados o comprados a proveedores externos. Además, nos ha ayudado a avanzar en la prevención de accidentes, creando componentes específicos para procesos muy concretos”.
Tras el éxito inicial de esta fase piloto, HEINEKEN valora escalar el proyecto a otras fábricas de todo el mundo y ampliar el uso de la tecnología de impresión 3D a otras modalidades de aplicación, aprovechando las ventajas de este método de autoaprovisionamiento de material de maquinaria.
Noticias más leídas
Más noticias del departamento economía y finanzas
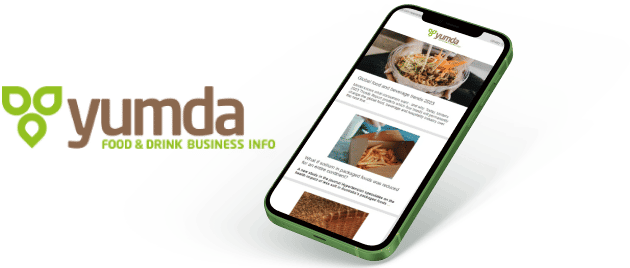
Reciba la industria alimentaria y de bebidas en su bandeja de entrada
Al enviar el formulario, se muestra usted de acuerdo con que LUMITOS AG le envíe por correo electrónico el boletín o boletines seleccionados anteriormente. Sus datos no se facilitarán a terceros. El almacenamiento y el procesamiento de sus datos se realiza sobre la base de nuestra política de protección de datos. LUMITOS puede ponerse en contacto con usted por correo electrónico a efectos publicitarios o de investigación de mercado y opinión. Puede revocar en todo momento su consentimiento sin efecto retroactivo y sin necesidad de indicar los motivos informando por correo postal a LUMITOS AG, Ernst-Augustin-Str. 2, 12489 Berlín (Alemania) o por correo electrónico a revoke@lumitos.com. Además, en cada correo electrónico se incluye un enlace para anular la suscripción al boletín informativo correspondiente.