Bosch extends Sealed Paper Packaging portfolio at interpack 2017
Ideal for products such as sugar and flour
Advertisement
- New vertical bagger adapted for handling innovative paper bags
- Dust-tight packaging available on upgraded mandrel wheel machine
- Sustainable packaging conserves resources and enables recycling
Further to the launch of the world’s first Sealed paper packaging on a vertical form, fill and seal machine (VFFS) with the ZAP-Module in 2016, Bosch packaging technology and BillerudKorsnäs are bringing their latest innovations to interpack 2017. On display for sugar manufacturers will be the SVE 2520 ZAP, Bosch’s first continuous-motion VFFS machine now capable of producing dust-tight, sealed paper bags. Flour producers will benefit from the upgraded PME mandrel wheel machine with ZAP-Module
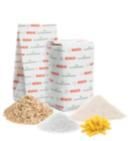
First mono-material paper bags produced on continuous-motion VFFS bagger and mandrel wheel machine
Bosch
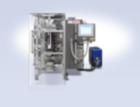
Continuous-motion vertical bagger now with ZAP-Module
Bosch
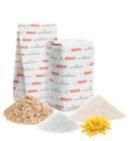
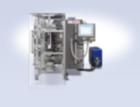
“The positive reaction of the market to the launch of Sealed Paper Packaging in 2016 led to an extension of the ZAP-Module within our portfolio. By offering two alternative technologies now equipped with the ZAP-Module, we are not only able to answer the individual needs of dry food producers, but also give them the possibility to differentiate themselves by offering consumers completely recyclable paper packaging – at the same time improving product quality,” said Bernhard Bruhn, product line manager dry food at Bosch Packaging Technology.
Sustainable revolution
Until now, the production of mono-material paper packaging was only possible with glued pre-made bags or formed paper bags on mandrel wheel technology. The VFFS concept, more flexible regarding formats and pack styles and thus popular on the market, previously only allowed bag production using polymer film or fully coated paper. With the ZAP-Module from Bosch it is now possible to process mono-material paper on VFFS technology with dust-tight sealing. The secret lies in the characteristics of the Axello®ZAP paper from BillerudKorsnäs, which was specially developed for this application, as well as in the ZAP-Module from Bosch Packaging Technology. Moreover, the ZAP-Module partially applies a minimal amount of the sealing agent during the packaging process enabling heat sealing of the paper on the VFFS machine. Now this new sealed paper packaging is also available for the mandrel wheel technology to improve the traditional paper bags produced on this type of machines by making them dust-tight. As a result, retailers and consumers profit from clean shelves, enhanced product protection from contamination and thus improved product quality.
Continuous-motion vertical bagger now with ZAP-Module
The extension of the ZAP-Module to the first continuous-motion SVE machine offers manufacturers significant production flexibility and enhanced product safety. By producing different bag styles (pillow, gusseted or block bottom) with different packaging materials (both Axello®ZAP mono-material paper and heat-sealable laminates) on the same machine it enables manufacturers to enter new markets for dry food applications. In order to achieve a perfect dust-tight sealing, the machine is equipped with the ZAP-Module for heat sealing of the paper. Additionally, the machine combines a small footprint with a speed of up to 65 bags per minute. By adapting the gusseting and dosing unit, the solution ensures gentle material processing and high efficiency. Based on the proven SVE technology, the solution allows easy operation and maintenance, helping manufacturers to adjust quickly to evolving consumer demands.
Upgraded mandrel wheel technology for a competitive edge
The combination of the robust mandrel-wheel concept with the ZAP-Module allows for the production of tightly sealed paper bags protecting flour from external contamination. By offering additional functionalities, such as the inline weighing system and top-up dosing, customers benefit from the highest weight accuracy available on the market. The increased flexibility of the solution allows to produce a wide range of package sizes and formats on a single machine. Another advantage of this technology is the outstanding shape of the block bottom bag, with a gable or flat top, thanks to double bottom-pressing which helps in forming a hard, brick-like bag. While achieving an output of up to 100 packages per minute, the vibrating module shapes the bag and closes it keeping the air out, thus simplifying product compaction. This enables manufacturers to optimize their storage capacities and logistics processes, thereby reducing their environmental footprint.
To learn more about Sealed Paper Packaging possibilities, visit Bosch at interpack in Düsseldorf, Germany, from May 4th to 10th, 2017, Hall 6, C58. Click here for more information.